Corrosion testing
What is meant by corrosion testing?
Corrosion is the reaction of a metallic material with its environment. This causes a measurable change in the material (corrosion phenomenon) and can impair the function of a component or an entire system (corrosion damage). In order to be able to simulate these environmental influences under laboratory conditions, we have a corrosion laboratory. We divide corrosion tests into three groups.
- harmful gas tests
In a noxious gas test, products are exposed to an atmosphere with aggressive industrial gasses, such as can prevail in industrial areas. By combining different gases, complex corrosion processes can be simulated. - salt spray tests
Salt spray tests can be used to simulate offshore use or the transport of your goods by sea. The saline atmosphere accelerates the oxidation of metals. Salt spray and climatic tests are combined to increase the effect of salt on metals. - condensation tests
These tests are used to accurately detect corrosion protection defects. They expose coatings of a material or system to a water vapour saturated atmosphere. If the coating is defective, moisture will penetrate and infiltrate the coating. The condensation test can be further enhanced by the combination of condensation and harmful gas.
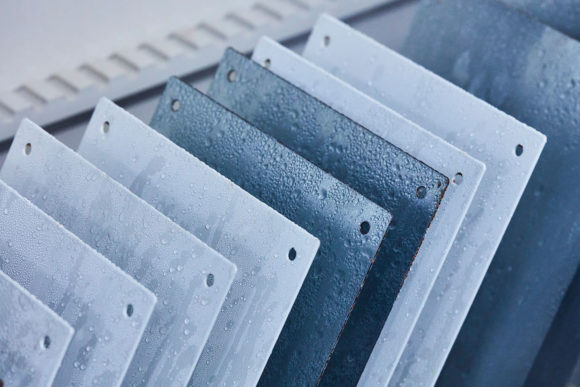
Range of services of our corrosion laboratory
We have facilities for all three corrosion tests. The combination of corrosion and climate tests is also possible thanks to our modern facilities. Tests with up to four harmful gasses can be carried out simultaneously in our harmful gas cabinets. By using hydrogen sulphide (H2S), sulphur dioxide (SO2), nitrogen dioxide (NO2) and chlorine (Cl2), we are able to simulate tests with the most common industrial exhaust gases. Concentrations between 5 ppb and 50 ppm and ambient conditions of up to 40 °C as well as a relative humidity of up to 95 percent are used. Harmful gas tests can be used, for example, to check contact corrosion on electrical components such as circuit boards or something similar.
For the exposure of your test sample to a salty environment, we have salt spray systems with a volume of up to 12 m³, which can also be used to test complete systems. A five percent NaCl solution is sprayed into the systems, which creates a dense salt mist around your test sample. This aerosol accelerates the chemical reaction of corrosion formation on your test specimen immensely. Testing with other salt compositions or concentrations is also possible in our facilities. In addition, we have equipment that allows a combination of climate and salt spray testing.
Furthermore, condensation water tests can also be carried out with our salt spray systems. These tests can be used to check coatings such as paintwork or galvanic surface changes. Due to the water vapour saturated atmosphere, possible weak points are undermined and lead to corrosion and an extension of damage under the coating. In order to be able to recreate this effect even more effectively, we have equipment that combines harmful gas and condensation water. Concentrations of up to 0.66 percent by volume of sulphur dioxide (SO2) are used here. The combination of sulphur dioxide and water produces the highly corrosive sulphuric acid.
We can also evaluate corrosion tests according to standardised procedures. Thus, we can evaluate the resistance of a coating system according to the degree of rust, the degree of blistering, the degree of flaking or with the help of a grid cut. In addition, we can offer you further investigations (e.g. macrosections, layer thickness measurement or similar) in our in-house materials laboratory.
Test lexicon
In the following table you will find some abbreviations for standardised test methods.
Abrevation | Meaning |
---|---|
Ka | Salt mist |
Kc | Sulphur dioxide (SO2) for electrical contacts and connections |
Kd | Hydrogen sulphide (H2S) for electrical contacts and connections |
Ke | Corrosion test with flowing mixed gas |
CH | condensation atmosphere, steady state |
AHT | Condensation atmosphere with alternating climate (alternating humidity and temperature) |
AHT 1,0 S | Sulfur dioxide test with general condensation of moisture |
AT | Condensation atmosphere with alternating climate (alternating humidity) |
NSS | Neutral salt spray test |
AASS | Acetic acid - salt spray test |
CASS | Copper-accelerated acetic acid salt spray test |
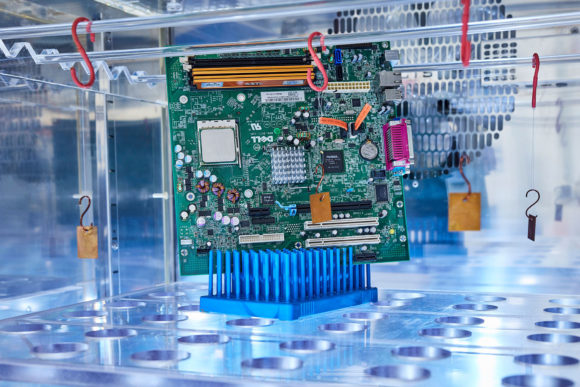

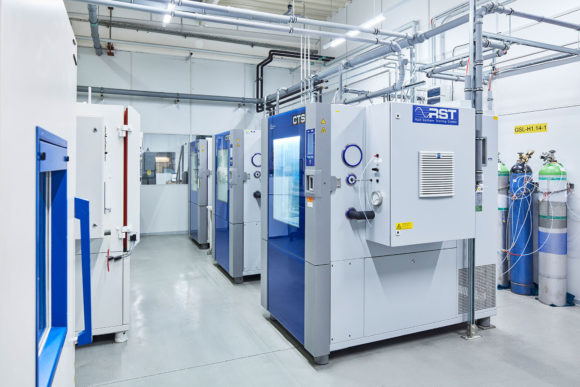
What are the advantages of corrosion testing?
Due to the use of different materials, corrosion can occur on your products even without external environmental influences. In order to eliminate these problems already in the development phase, we carry out accelerated corrosion testing for you. Furthermore, the tests can be used to simulate further possible applications for your products.
Are you in need of corrosion testing?
We would gladly support you. Contact us for testing.